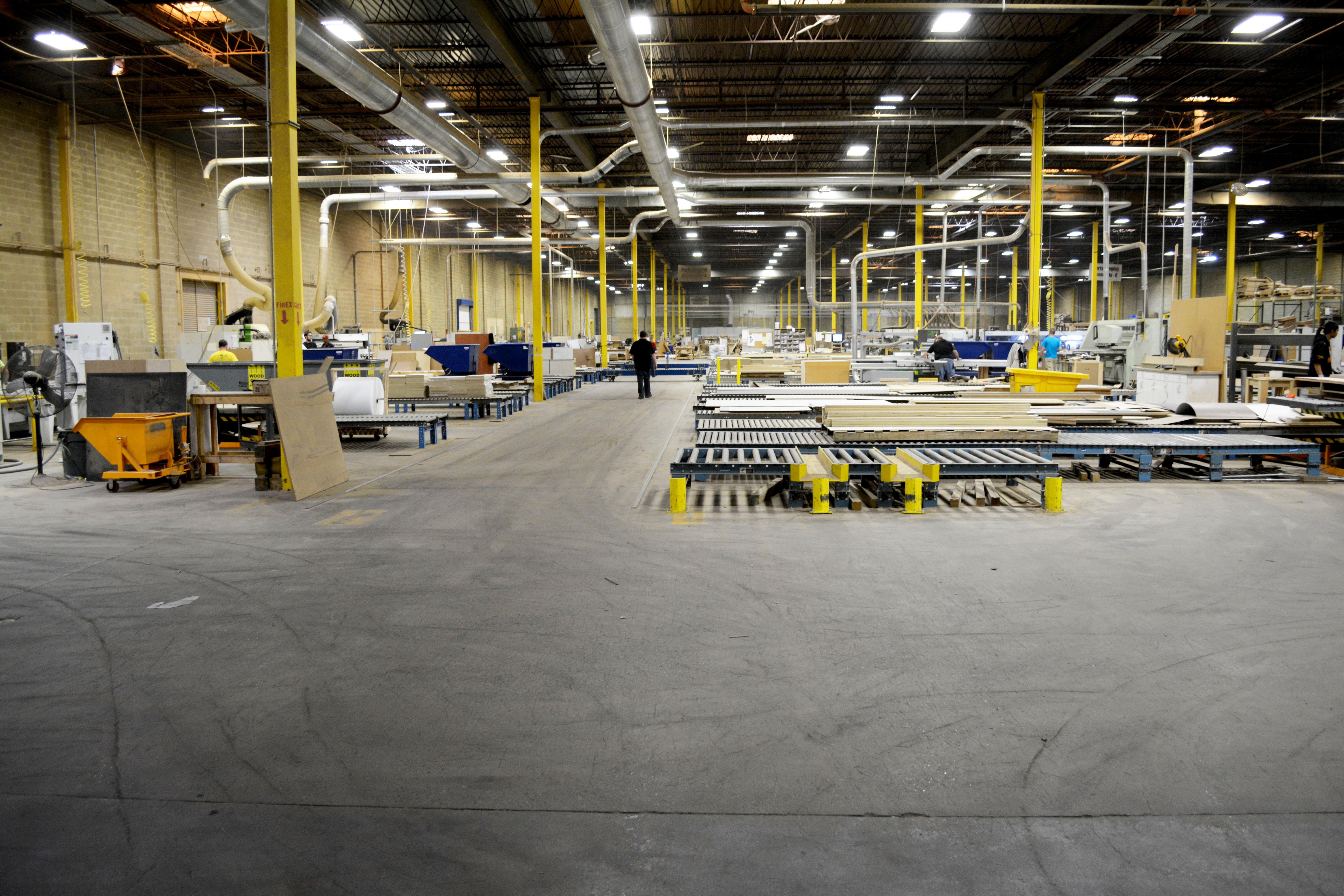
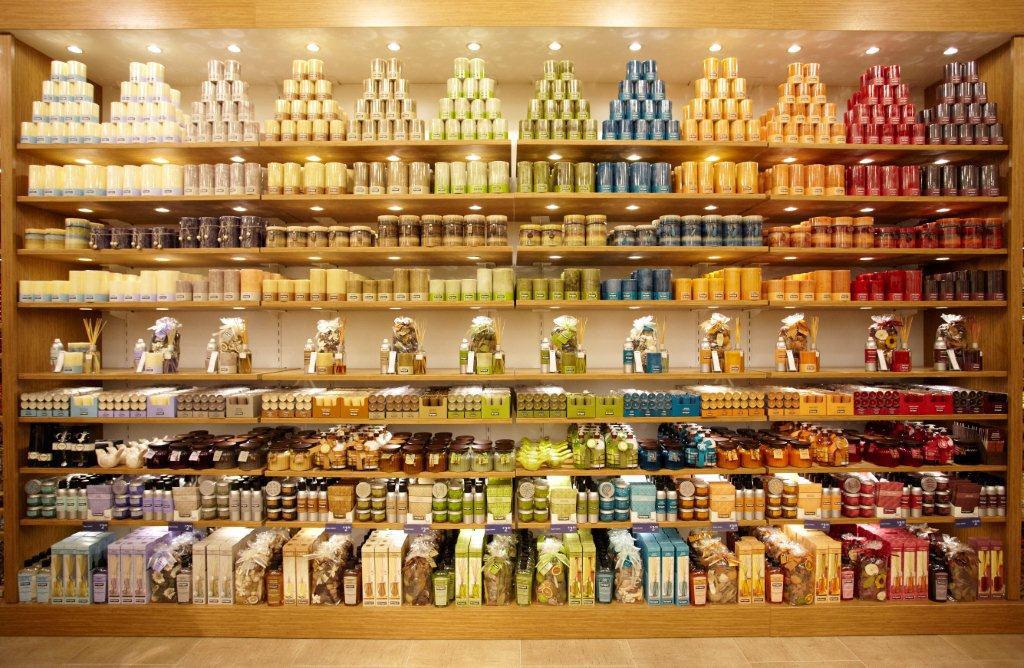
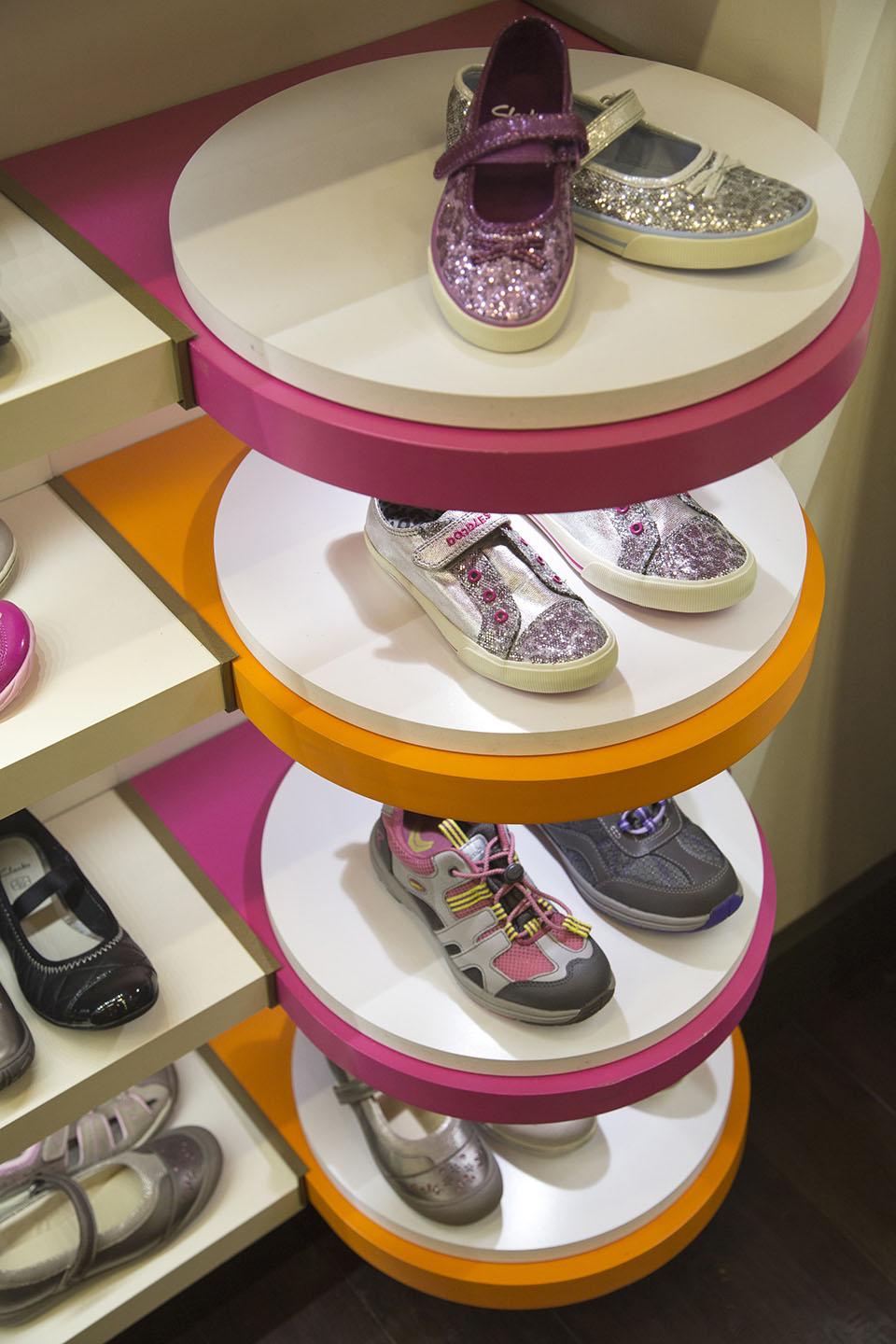
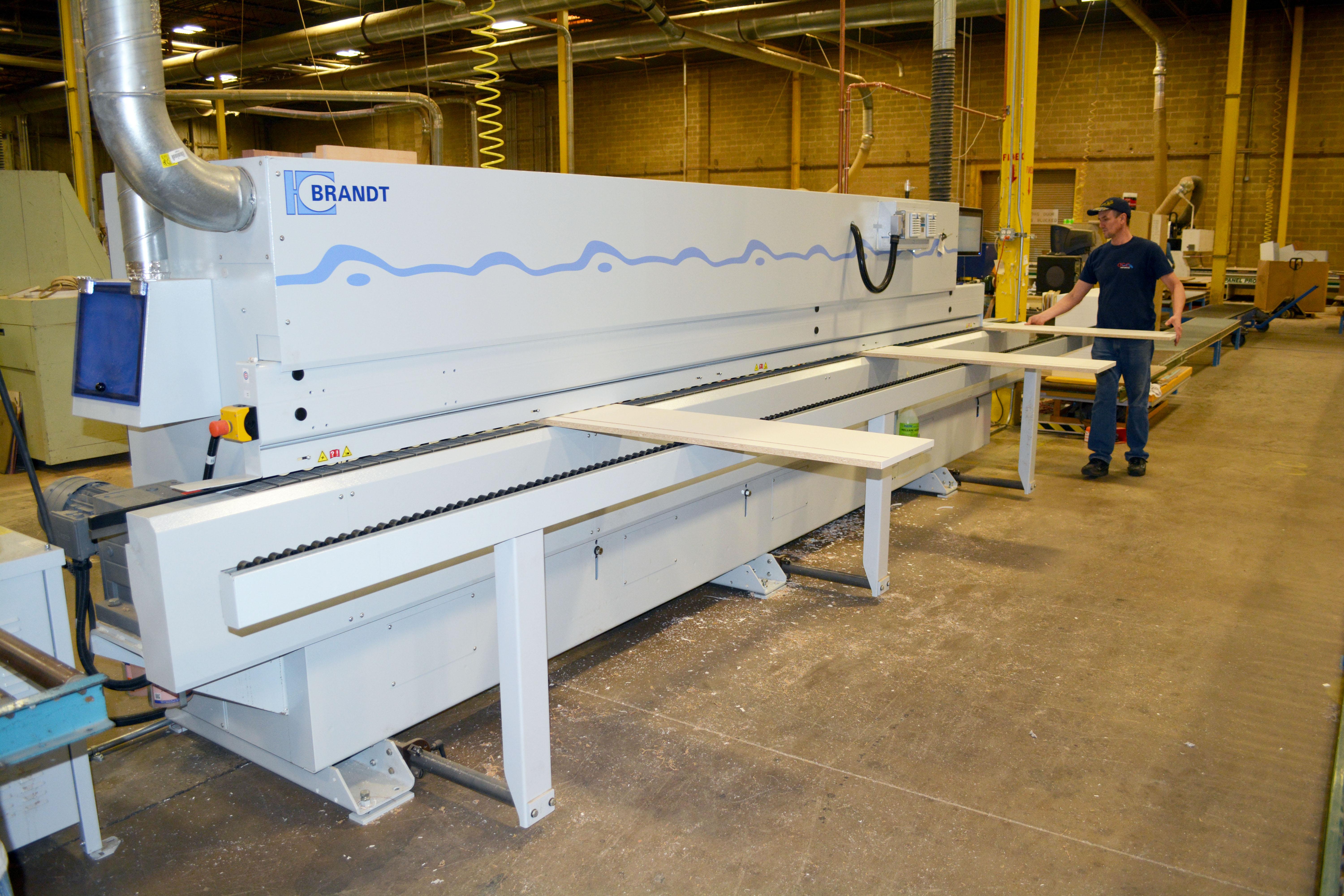
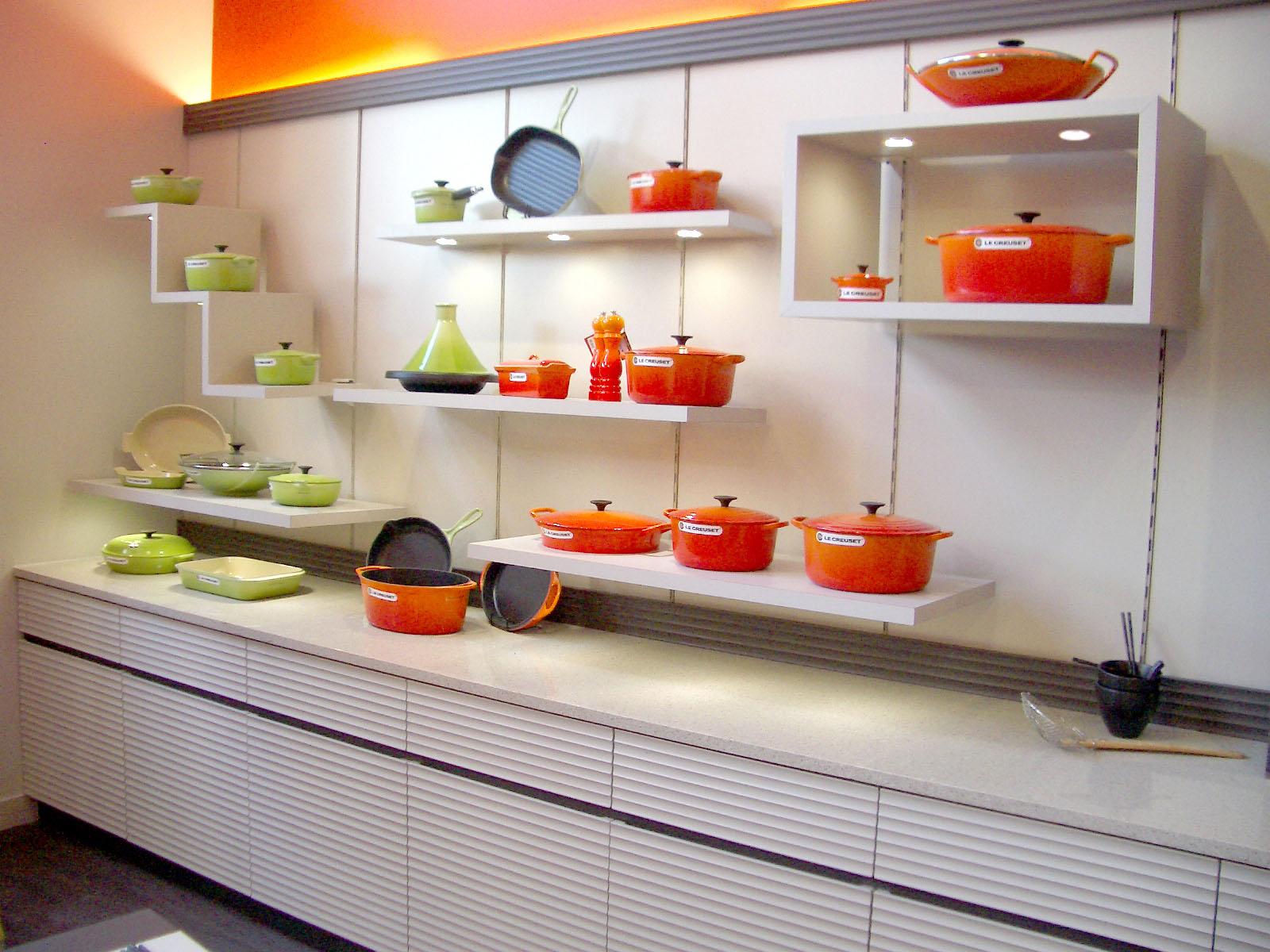
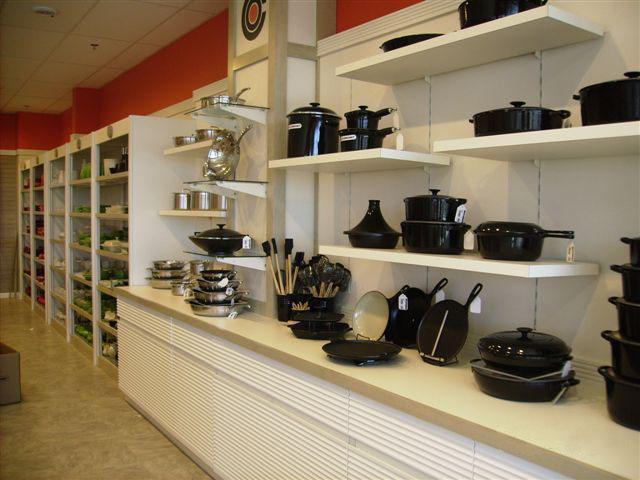
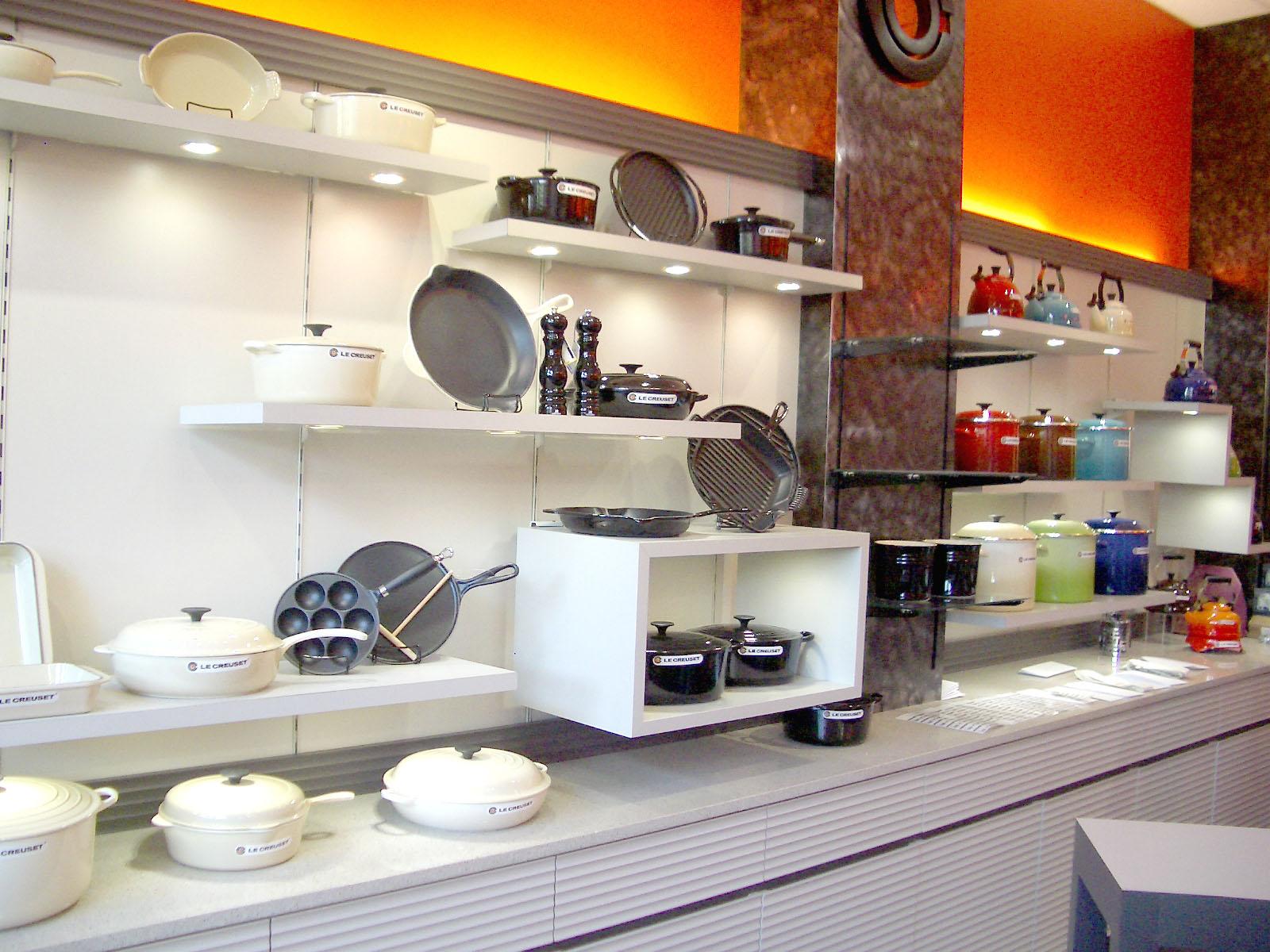

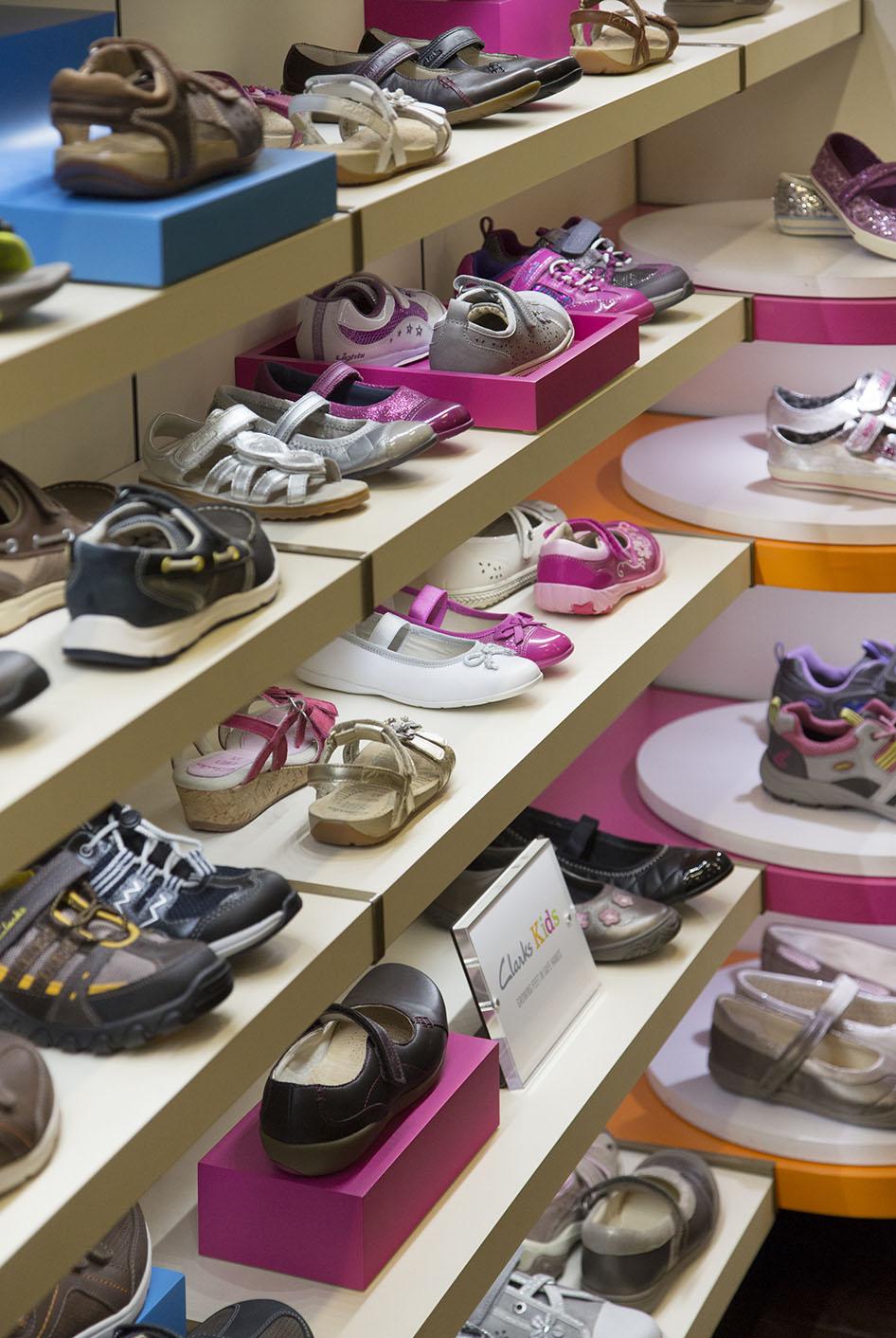
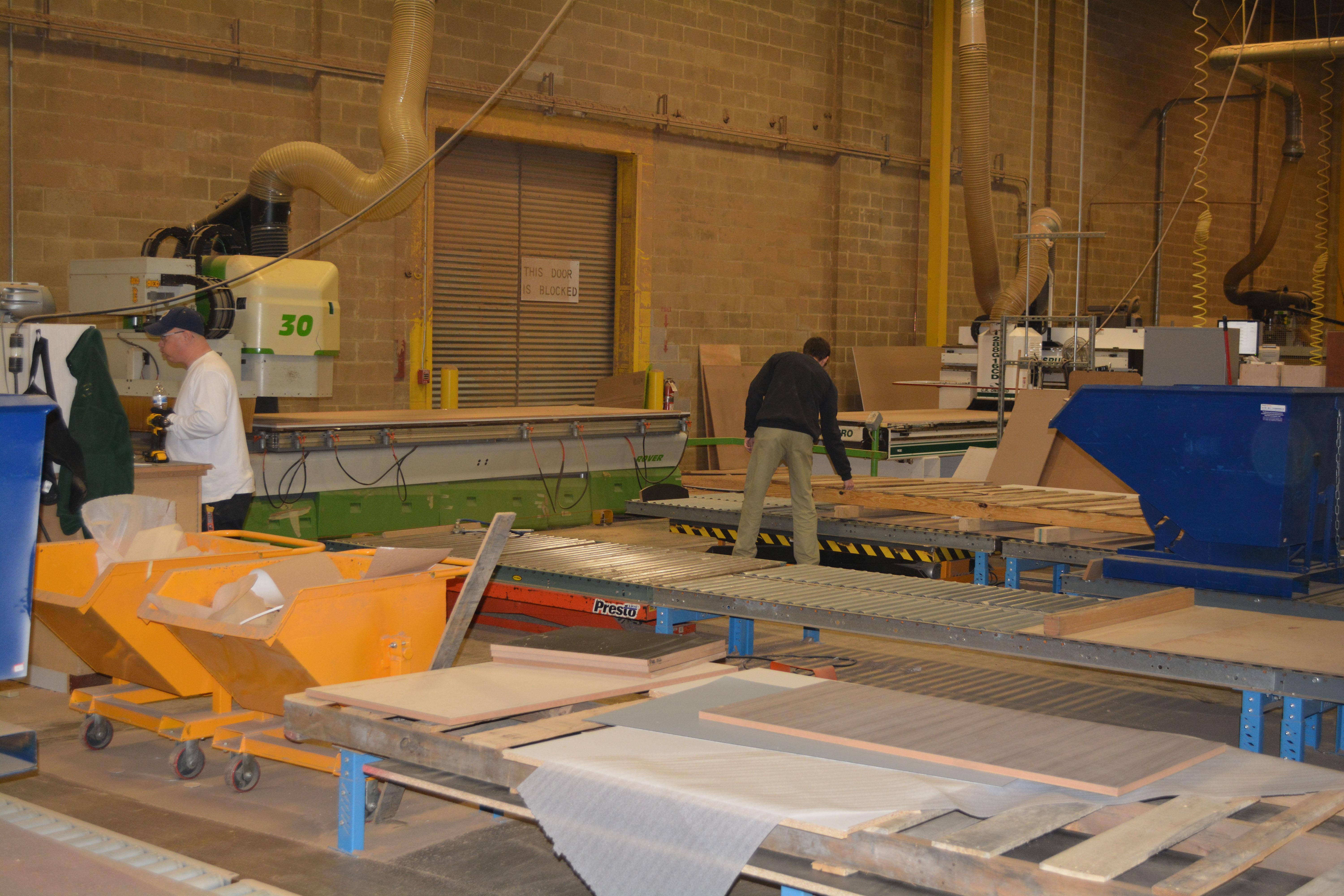
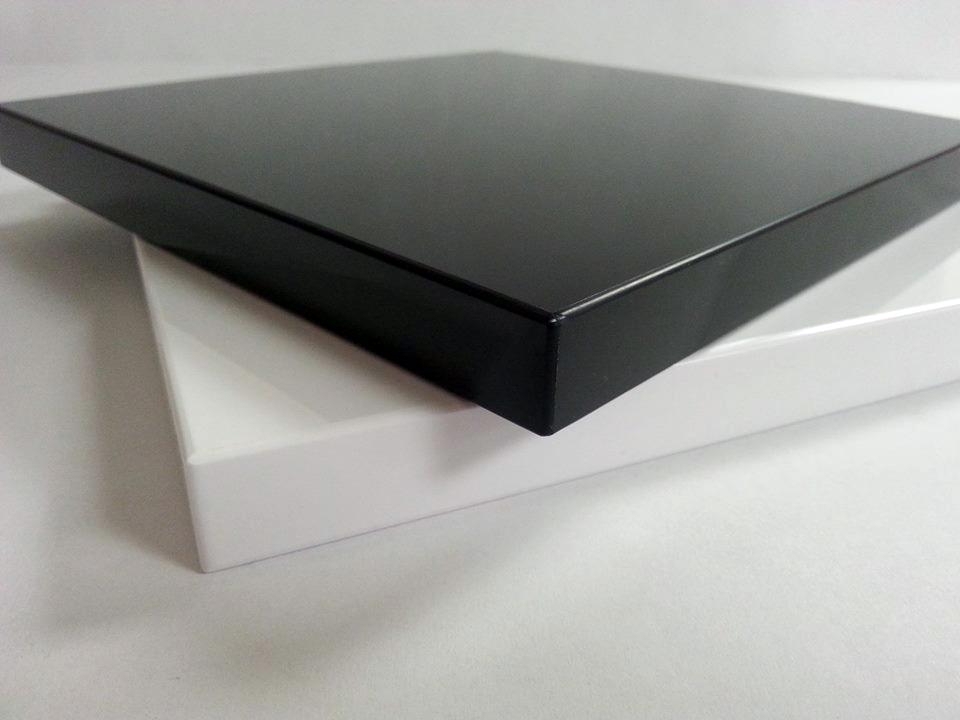
TC Millwork is one of those companies that constantly strive for improvement. Innovative and forward thinking, the company owners are very candid about always looking to the future for new technology and new product development.
Founded in 1993, TC Millwork is a full-service manufacturer of store fixtures, architectural millwork and commercial casework. Brothers and Co-owners/ founders Art and Dennis Kubach manage all aspects of the firm, which offers a full range of services for a diverse group of markets, including retail, casino and healthcare plus commercial casework. A short list of their retail clients includes many well-known companies, such as: Pier 1, Clarks, Whole Foods, David’s Bridal, Cato, Kicks USA, Yankee Candle, Wine & Spirits and Home Essentials.
“Our services include design, engineering, manufacturing and installation,” says Art Kubach. TC Millwork’s headquarters is in Bensalem, PA, a Northeast suburb of Philadelphia. The plant encompasses 430,000 square feet and has 85 employees. The company also has an office in Xiamen City, Fujian Province, China, which helps position it to provide competitive, offshore pricing for clients’ metal, wire, and acrylic needs, Kubach says.
Among the innovative products offered by TC Millwork are the patented Ven4ma, Thermaflex and SMARTWALL. Thermaflex is made from PVC film, thermally fused to a rigid MDF core and is used to produce trims, signs, shelving, panels, counters, soffits and more.
“It is durable and won’t crack, chip or delaminate and is a good choice for curves, rounded corners and 3-D effects” Kubach says of the product.
For areas where extra-impact protection is necessary, TC Millwork recommends VEN4MA, which offers a “durable combination of our PVC film fused over a rigid PVC core and is ideal for mall fronts, base trim, shelving and more.”
SMARTWALL is a low voltage, highly customizable display system that can be configured and manufactured to a client’s specifications and merchandising needs. Elements include puck or strip lights and floating or thin-line standard shelving.
“SMARTWALL is basically a wireless integrated wall system using LED lighting that allows a user to move product anywhere on the wall,” Kubach says.
“There are no restrictions with it. You can bring light anywhere you want it and include an integrated touch-screen powered off the wall. It is all self-contained and integrated. SMARTWALL can be used in other custom applications such as soffits, column wraps, gondolas and multi-tiered lit tables,” says Kubach. The response the product, he adds, has been “phenomenal.”
Production Enhancement
TC Millwork’s facility is equipped with machinery from many different manufacturers including Biesse, C.R. Onsrud, Weeke, Holzma, and Koch.
To further enhance its production capabilities, TC Millwork recently added a Brandt airTec 1600 hot air edgebander.
“We are very excited about this acquisition. For us it was the last piece of puzzle in offering the best in panels,” Kubach says. We had been interested in utilizing the zero-edge technology but weren’t sold on a laser because of the expense and the fact that laser edgebanders can be high maintenance. Within the last year, super heated hot air sytems offered another option.”
With the Brandt airTec edgebander, Kubach says, “We felt we had half of the equation with what we were using in our shop. This technology gives us the other piece. It lets us do virtually invisible seams. It also gives us the ability to create an additional market,” he added. “One of our goals is to be in as many markets as we can.”
Using the airTec unit, co-extruded edges are reactivated with hot air, which achieves a joint-free and zero glue joint. The compressed air “hits” the edgeband at about 500 degrees to activate a glue layer, then rapidly cools to approximately 120 degrees, allowing for quick machining of the panel.
“We see this technology as having great potential. It definitely produces a high-end product. Europe has embraced it for cabinetry, and we also saw its potential for retail. It has applications for flat and 3-D products. It not only offers a more visually appealing product without the joint, it offers a more durable product,” Kubach says.
Next on the horizon for the company is 3-D printing, particularly in the design phase of the project, Kubach says. “We think 3-D printing will be huge in the future and a great tool for producing prototypes.”
He adds, “Our company is constantly looking to the future. We feel it gives us an advantage.”
Jo-Ann Kaiser has been covering the woodworking industry for 31+ years. She is a contributing editor for the Woodworking Network and has been writing the Wood of the Month column since its inception in 1986.
Have something to say? Share your thoughts with us in the comments below.