As a professional woodworker, I have learned there are several instances where it is actually more efficient to shut production down temporarily. To be more specific, I mean it can have a positive impact on your productivity and your profits. I thought it would be wise to share with you young professionals some of my experience.
There are a few obvious reasons why you would want to shut production down, such as a family emergency, machines malfunctioning, or a serious injury. I’m not going to cover those because they are self-explanatory. The two main reasons I want to talk about are machinery maintenance and new machinery set up/retooling.
Maintenance shutdowns
Maintaining your machinery is a very important aspect of keeping your business running. How often you should do so depends on how hard you work your machines. It also depends on what types of machinery you run. If you have machines that are running nonstop on a daily basis, I suggest you shut down one day a month and do nothing but maintenance on your machinery.
This can involve everything from just cleaning it out and getting dust out of places that can rust, oiling gears, checking belt tension, or even cleaning your blades and cutters of pitch. It really depends on the specific machines.
For instance, I know my 20-inch planer requires some of the gears be oiled after a certain amount of hours of use, it is a special oil I have to order. If the machines in your shop are not running nonstop every day, it is likely you can get away with doing your maintenance and cleaning less often than monthly.
I am a smaller sized shop, so I typically do heavy maintenance quarterly. When I do that maintenance, I am extremely thorough. I take the time to clean and wax all my cast-iron tops. I also go through every single machine and remove every speck of dust and debris. When I am finished all of my machinery looks brand new — at least for a while.
Taking this time to fine-tooth comb your equipment can also reveal small problems that are starting to occur that you could have missed. Doing this has saved me a lot of money, catching stuff before it gets really bad.
If your shop is as busy as mine, it is easy to get caught up in the rhythm of working nonstop and forget that the machinery also requires downtime and maintenance. However, I urge you to be mindful of this and maintain your equipment.
There’s nothing worse than having a machine go down and the problem could have been prevented by routine maintenance. When this happens, your downtime is typically far worse than if you had just taken a scheduled day every now and then to perform routine maintenance.
This is what I mean by helping your profits by doing maintenance. Remember your machines are also employees, they require care and oversight. To get a better idea of what your machinery needs regarding maintenance, it can usually be found in the instruction manual that comes with it or finding one available online. When in doubt ask a more experienced professional to take a look or for specific suggestions based on your needs.
Retooling and new machinery
The other reason for a temporary production shutdown is for retooling and new machinery set up. There have been several times in my career when stopping production in the middle of work to purchase and install a new machine actually made the job finish ahead of schedule. This was completely dependent on the fact that the machine I was bringing in made that job go faster.
If you’re making good machinery purchases, something we’ve already covered in previous articles, then losing a day or two to install a machine can actually gain you up to a week in production.
I have also found that I don’t like working in a cluttered, messy workspace. Nothing is more unorganized and messy than furniture parts that I’m working on mixed with machinery parts and dust collection fittings all over the place. It is an extremely inefficient way to work.
The perfect scenario is bringing new machinery in between jobs or when you have downtime. Unfortunately, the reality of a busy shop is that is rare and often imperfect in timing. So, when I bring in a new machine, I typically halt my production right where I’m at on the workpiece, put everything away in an organized fashion (including the labeling of parts), and clean. Then I will bring in the new machine to focus on getting it set up in every way before going back to work.
Now if you're like me and tend to buy multiple machines all at one time, then I really suggest shutting down production and knocking that out as fast as you can.
Renting equipment, hiring pros
As a Young Wood Pro, it is fair to assume that your workspace is a smaller workspace and has smaller production output. That’s relevant because it’s also likely you don’t have a forklift, and that’s alright, neither do I. I typically rent one to help unload and place my machinery in its final destination.
In the spirit of efficiency and making the rental fee of the forklift worth it, I like to go ahead and get all my new machinery bought and moved in one run when I can. Don’t get any crazy ideas, this is not an annual event around my place. Every few years I upgrade or as necessary per job. I promise you that shutting down for something like this is wise. Having work pieces everywhere with machinery installation stuff and dust fittings as mentioned before is only amplified and worse with multiple machines. It also makes it easier on your electrician when coming in to wire it all up. This typically results in a cheaper bill and the electrician being more willing to help again in the future.
I know how counter intuitive it seems to shut down production in a profit based situation. For someone who’s new in this business, it probably sounds like an insane idea.
However, I urge you to heed my words and experience. I do hope as your career moves along and you upgrade your machinery over time, my suggestions will be helpful. Also, always remember that the machinery you’ve invested in does require maintenance, and it’s not to be taken lightly. As chaotic as it sounds it is a high-class problem for us woodworkers.
Installing new machinery can be extremely stressful, and continuing the maintenance on it can be stressful as well. The good news is if these are our problems as professionals, it means we a growing, and business is good. I call these high-class problems, but not ones that we can afford to ignore.
#YoungWoodPro is a contest and an educational program sponsored by Grizzly Industrial to help novice professionals improve their skills in business and woodworking.
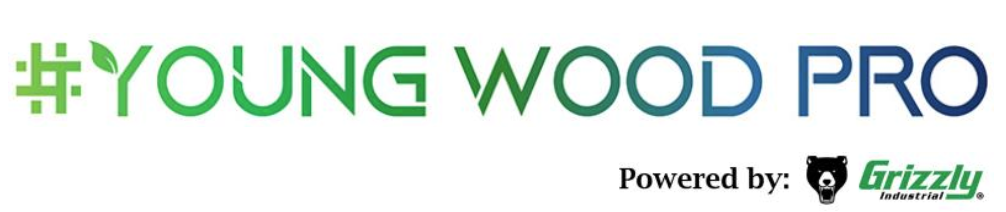
Have something to say? Share your thoughts with us in the comments below.